A recent CPI report analyzes the cost of CO2 abatement and the impact on material production costs of low-carbon technologies for decarbonizing India’s steel and cement sectors. Well-designed policy frameworks will be critical to support technology adoption.
(This piece is a follow-up to our previous blog, “The Path to Decarbonizing India’s Steel and Cement Industry” which lays the context and highlights the urgent need for strong public policy and financial interventions in India to align two of the country’s largest CO2-emitting industrial sectors—cement and steel—with long-term, low-carbon pathways.)
While India is doing well in transitioning towards a low-emission electric sector, it needs to massively step-up efforts to ensure low-carbon growth of hard-to-abate industrial sectors. Steel and cement are two of the most emissions-, energy-, and capital-intensive industries in India, and industrialization and urbanization are rapidly increasing the demand from these sectors. Our estimates shows that the total installed production capacity in these sectors could grow between 2 to 2.5 times by 2040. Meaning, India needs to immediately deploy all the available low-carbon solutions (LCS) at its disposal, to keep the emission trajectory from these two sectors consistent with its long-term targets and global climate ambitions.
Decarbonizing steel and cement production will require a host of LCS comprising several supply-side technologies and some demand-side measures. Currently available LCS, like scrap-based secondary steel and composite cement, remain under-utilized due to market, regulatory, or financing barriers. Other high-impact LCS, like green hydrogen and carbon capture technologies, are currently commercially unviable. Our recent assessment of LCS for the steel and cement sectors suggests that, despite these limitations, it is possible to mitigate about 50% of the cumulative emissions from the new steel and cement production capacity that will be added between now and 2040. Under this scenario, transitioning the additional new capacity to a lower emission intensity would cost the steel and cement sectors (at least) an additional USD 100 billion and USD 65 billion respectively.
A deeper analysis of the techno-economic profiles of individual technology-oriented LCS sheds further light on their potential application in the Indian steel and cement sector. To build this profile, we consider three key characteristics of these LCS, which critical in policy-making and investment decisions:
- Potential to reduce the emission intensity of production (of steel/cement) – a measure to assess climate impact.
- Cost of CO2 abatement (CoA)[1] – a measure to assess relative economic efficiency of CO2 abatement across different LCS.
- Impact on levelized cost of production (of steel/cement) – a measure to assess impact of LCS on industrial competitiveness.
Key findings from our recent assessment:
STEEL SECTOR
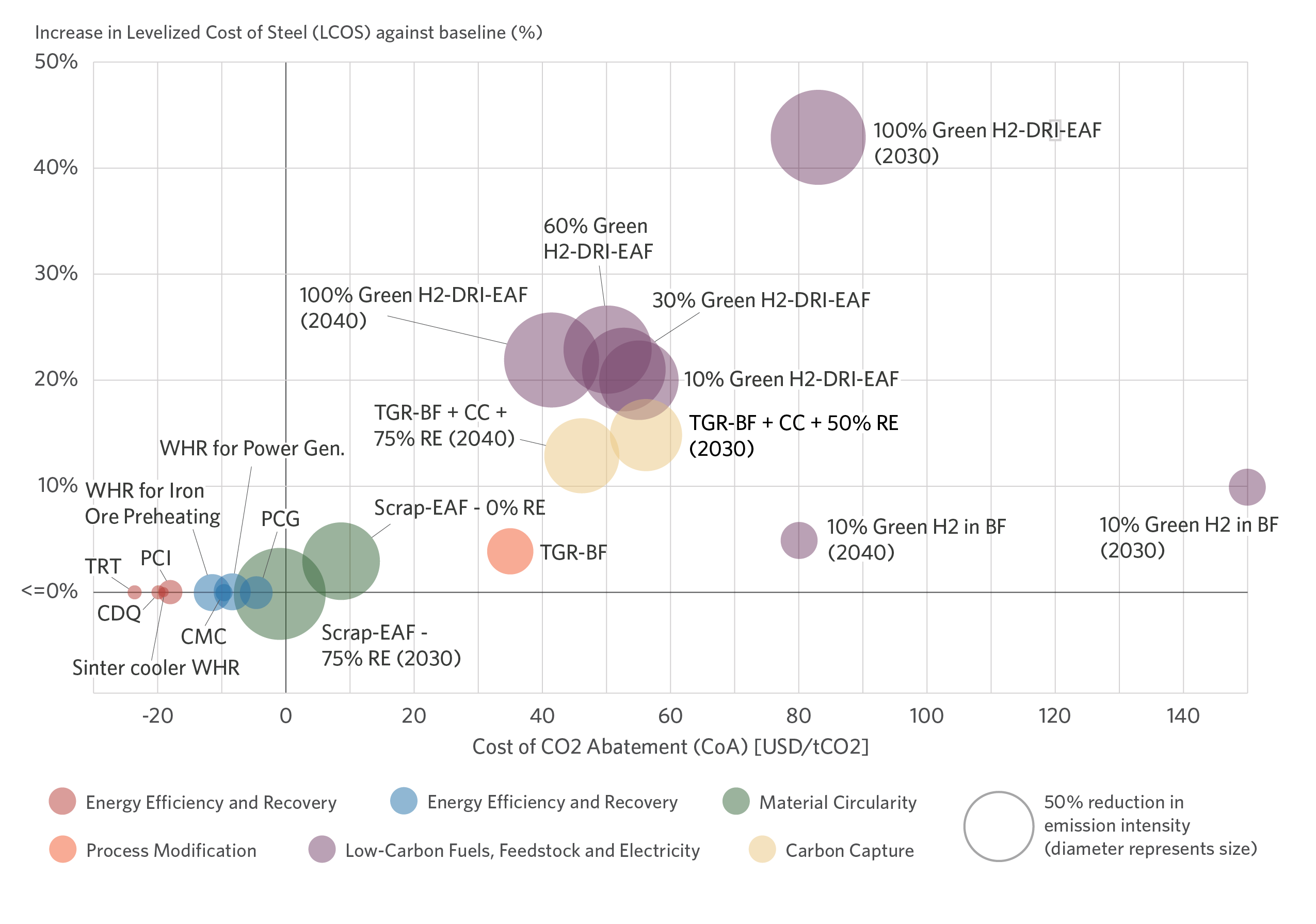
Figure 1: Cost of CO2 abatement (CoA, X-Axis), impact on levelized cost of steel (LCOS, Y-Axis) and potential to reduce CO2 emission intensity of production (size of bubble) of low-carbon technologies for steel sector, compared to baseline coal-based DRI-EAF and BF-BOF routes.
Abbreviations: DRI = Direct Reduced Iron, BF= Blast Furnace, EAF = Electric Arc Furnace, RE = Renewable Electricity, CDQ = Coke Dry Quenching, TRT = Top Pressure Recovery Turbine, PCI = Pulverized Coal Injection, WHR = Waste Heat Recovery, H2 = Hydrogen, CC = Carbon Capture, TGR = Top Gas Recovery.
Source: CPI Analysis.
- Indian steel industry is more emission intensive than the global average. There is significant potential for deployment of existing energy efficiency and recovery technologies, but their potential for climate mitigation remains limited. The CoA of these technologies is negative, implying CO2 mitigation is achievable while having negligible impact on the cost of production. However, these technologies can cumulatively reduce the emission intensity of production by about 10-20% and therefore will likely not play a central role in sectoral decarbonization in the long-term. Of the available options, the largest potential lies with Waste Heat Recovery technologies that reuse waste heat for thermal processes or electricity generation. However, high capital expenditure and long payback periods remain a barrier to adoption, especially in the SME sector.
- Scrap-based EAF route for the production of secondary steel is a highly effective lever available to steelmakers. This alternative route for production of secondary steel has a very high potential of reducing emissions intensity by 60% – 85% (depending on the use of renewable electricity and storage for powering the EAF), a low CoA less than 10 USD/tCO2, and negligible impact on the cost of production of steel. However, long-term availability of low-cost scrap in the country is a key challenge for new capacity addition through this route.
- Partial use of green hydrogen in gas-based DRI (up to 60%) is one of the leading technology candidates for production of lower-carbon steel during the transition period. Using between 10% to 60% green H2 in DRI (remaining share being natural gas) is technically feasible and has the potential to reduce emission intensity by up to 80%, compared to traditional coal-based DRI. Due to supply constraints and expected price volatility in global natural gas markets, and availability of cheap RE, this technology is an attractive option for Indian producers during the transition-phase, until a shift to 100% green hydrogen becomes feasible. However, at current costs of green hydrogen production (~5 USD/Kg), the CoA of about 50 USD/tCO2 and an increment in LCOS by 20-25% (depending on share of green hydrogen) is to be expected, which will negatively impacting the competitiveness of the industry. Although rapid decline in cost is expected over the next two decades, significant interventions in form of price support, low-cost capital, and creation of market demand for low-carbon steel will be needed to incentivize adoption.
- Top Gas Recycling Blast Furnace (TGR-BF) and smelting reduction (HIsarna) are the top alternatives to traditional BF for capacity addition during the transition period. Both technologies can be combined with carbon capture in the long-term. TGR-BF and HIsarna have 20-25% lower emission intensity compared to traditional BF route. The CoA and impact on LCOS are also relatively low at about 35 USD/tCO2 and +5% respectively and would decrease further with technological learning. Both these technologies are currently in demonstration stage and market entry is expected by 2030. TGR-BF and HIsarna can also be coupled with carbon capture technologies, which more than doubles their CO2 mitigation potential. But due to high costs and barriers associated with carbon capture, this option is unlikely to be deployed at scale before 2040. Even by 2040, the CoA for TGR-BF and HIsarna with carbon capture could be around 40-50 USD/tCO2, necessitating comprehensive policy support, innovative financing solutions and enabling market conditions to ensure viability.
- Green hydrogen can be used partially in traditional BF as feedstock to replace coal/coke as a reducing agent but is expected to remain uneconomical. Hydrogen injection can achieve about a 15-20% reduction in emission intensity compared to tradition BF route. However, at the current green H2 cost of ~5 USD/Kg, the CoA is very high at about 450 USD/tCO2. Even assuming a rapid decline in the cost of green hydrogen to 2 USD/Kg by 2040, the CoA would only decline to 80 USD/tCO2. Therefore, this technology would likely remain unviable without significant innovation breakthroughs or strong policy interventions that can bridge the viability gap.
CEMENT SECTOR
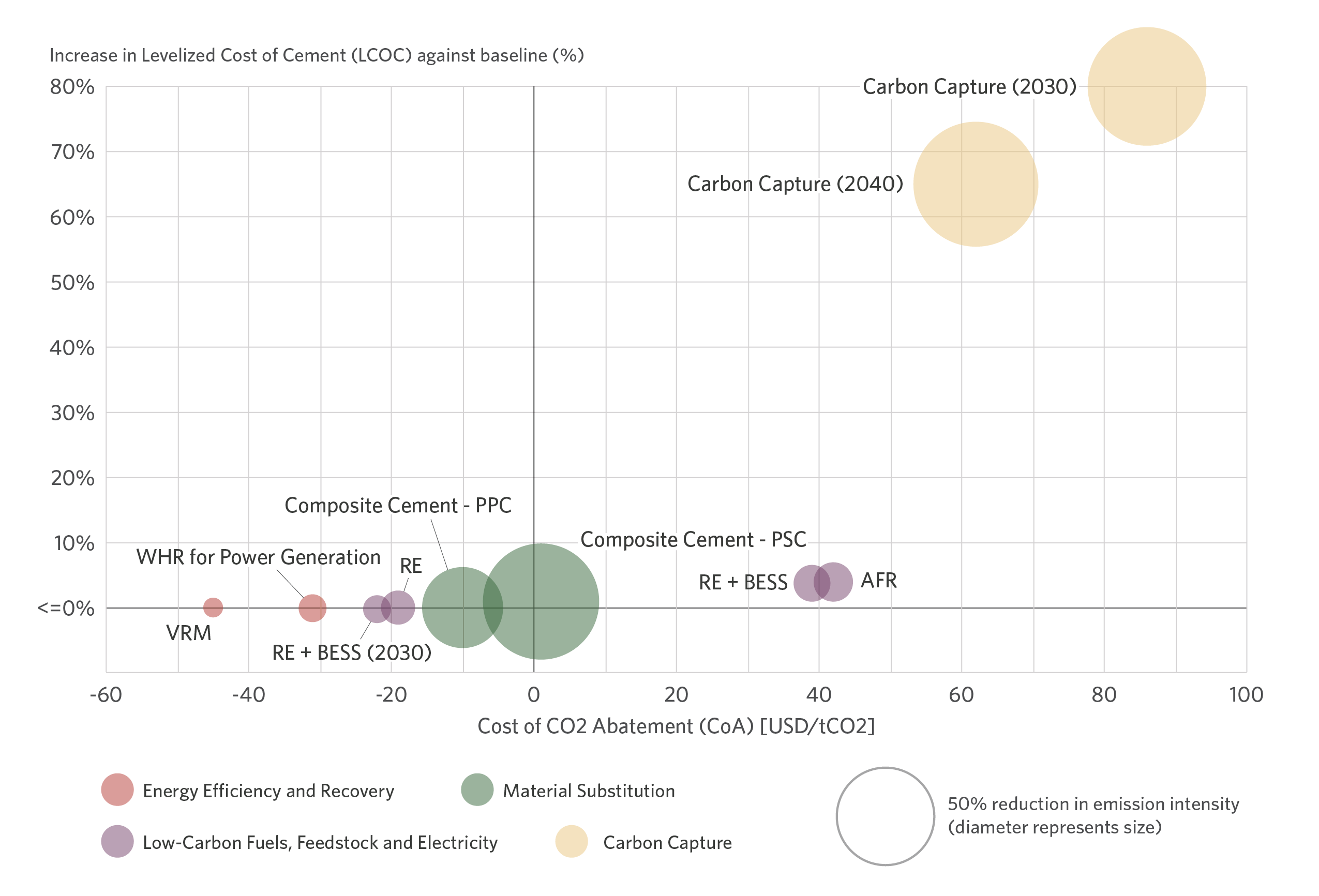
Figure 2: Cost of CO2 abatement (CoA, X-Axis), impact on levelized cost of cement (LCOC, Y-Axis) and potential to reduce CO2 emission intensity of cement production (size of bubble) of low-carbon technologies for cement sector, compared to baseline production route.
Abbreviations: VFD = Variable Frequency Drives, VRM = Vertical Roller Mills, WHR = Waste Heat Recovery,
RE = Renewable Electricity, BESS = Battery Energy Storage Systems, AFR = Alternate Fuels and Raw Materials,
PPC = Pozzolan Portland Cement, PSC = Pozzolan Slag Cement.
Source: CPI Analysis.
- Production of composite cement, Pozzolan Portland Cement (PPC), and Pozzolan Slag Cement (PSC), using waste materials like slag and fly ash, is an economical low-hanging solution for the cement sector with a very high potential to mitigate CO2 emissions. Shifting to production of PPC and PSC entails negative to near-zero CoA and has a large emission reduction potential of up to 35% and 70% respectively (depending on clinker substitution rate), compared to production of Ordinary Portland Cement (OPC). However, several supply-side barriers related to availability and sourcing of materials, and demand-side barriers related to consumer awareness and lack of standardization on use of composite cement need to be addressed to promote widespread adoption of composite cement.
- The Indian cement industry is more energy efficient and less emissions intensive than the global average. However, there is limited scope for the adoption of energy efficiency and recovery technologies. Indian cement industry has already adopted most major energy efficiency technologies. While these technologies have a negative CoA, cumulatively, they can only reduce emission intensity up to 10% and would likely play a marginal role in sectoral decarbonization in the long-term. Of these technologies, Waste Heat Recovery is the most promising in terms of emissions reduction and deployment potential.
- Use of alternative fuels in kilns (AFR) and electricity supply from RE and battery energy storage systems (BESS) are low-cost options available to producers in the near-term, but have a limited potential to abate emissions. The use of RE (for meeting up to 30% of electricity needs) is now more economically attractive than captive thermal plants. A higher share of RE use (up to 75%) can be achieved with BESS but this option is currently unviable, having a CoA of 40 USD/tCO2, mainly due to the high cost of storage. Use of AFR (at a thermal substitution rate of 25%) also has a similarly high CoA due to the significant costs associated with equipment, segregation, and processing of waste before use. With a rapid decline in storage costs, RE with BESS could become economically viable by 2030. However, these options can cumulatively reduce the emission intensity by just about 15%, due to limitations in use of AFR and a low share of electricity consumption in the overall emissions from cement production.
- The most important lever for long-term deep decarbonization of the cement sector is carbon capture, but market entry is expected only by 2035-2040. There are several proven carbon capture technologies available that can mitigate between 70% to 90% of direct emissions from cement production. However, the current CoA is about 100 USD/tCO2 (nearly 50% more than the steel sector). Market entry in India is expected by 2035-2040, by when the CoA is expected to fall to 60 USD/tCO2. Even then, this technology would be unviable without presence of high-value CO2 utilization markets, storage options, and supporting infrastructure, all of which would require targeted policy support and innovative financing interventions.
KEY RECOMMENDATIONS AND TAKEAWAYS FOR POLICYMAKERS
Development and deployment of the low-carbon solutions face a diverse set of country-, sector-, and technology-specific barriers. Policies have a crucial role to play in addressing these barriers and supporting the industry in its low-carbon transition. Key policy recommendations, based on our analysis of low-carbon solutions, include these market-based, fiscal, and regulatory measures:
- Strengthen international collaboration with governments and technology suppliers for indigenization of technologies and intellectual property.
- Provide innovation grants and form public-private partnerships for demonstration pilots of early-stage, commercially unviable, and capital-intensive technologies.
- Develop sector-level long-term decarbonization pathways, in consultation with the industry. Such pathways much include elements such as definitions of green steel and green cement, potential decarbonization levers and barriers to adoption, interim and long-term decarbonation targets, and the role of the public and private sectors.
- Planning and public capital outlay for the development of crucial supporting infrastructure such as pipelines for transportation of H2 and CO2, and industrial hubs.
- Implement a carbon pricing mechanism, either as a tax or a cap-and-trade market. Most high-potential low-carbon technologies have a CoA between 30 – 100 USD/tCO2. If designed well (to ensure stable and sufficiently-high price on carbon), carbon pricing can be a highly-effective tool to improve the viability of investments in innovative technologies and accelerate the pace of transition. Border adjustment mechanisms can be applied to prevent harm to the competitiveness of the domestic industry.
- Provide price support (as green premium) to producers of low-carbon steel and cement by creating initial markets through public procurement schemes, contract-for-difference (CfDs), or standards for end-use sectors.
- Implement a sustainable finance taxonomy combined with targets for financial institutions to monitor, disclose, and improve on the carbon-intensity of their portfolio comprising of investments in emission-intensive sectors.
- Establish technology standards for efficiency technologies, Renewable Electricity, Battery Energy Storage Systems, Alternate Fuels and Raw Materials.
A detailed analysis of the techno-economic profiles of low-carbon technologies discussed in this piece can be found in our full report.
To get the full report, please write to admindelhi@cpiglobal.org.
[1] Estimates for greenfield investments: excludes costs associated with funding for research and demonstration pilots, and supporting infrastructure required for transportation and storage of low-carbon fuels and captured CO2. Therefore, the actual cost of abatement would be higher than discussed here.